Refined C5 petroleum resin for hot melt road marking paint
Refined C5 petroleum resin for hot melt road marking paint
If you need COA or TDS, please fill in your contact information in the form below, we will usually contact you within 24 hours. You could also email me info@longchangchemical.com during working hours ( 8:30 am to 6:00 pm UTC+8 Mon.~Sat. )
1. Light color; good fluidity; high wear resistance; the filler is evenly dispersed and does not settle
2 Petroleum resin hydrogenation catalyst
Catalytic hydrogenation is an important technical way to produce high-end petroleum resin, and the development of efficient and stable resin hydrogenation catalyst is a key technical link. Aiming at the characteristics of petroleum resin containing impurities such as sulfur and halogens, large spatial site resistance of resin molecules, and easy to crack at high temperature reaction, researchers have focused on studying the influence of catalyst composition, structure and surface interface properties on active site distribution and hydrogen dissociation ability, improving the catalyst's toxicity resistance, hydrogenation activity and stability, and upgrading the quality of hydrogenation resin, so as to lay a foundation for its application in the industrial production.
Resin hydrogenation catalysts are mainly divided into three types: precious metal catalysts, non-precious metal catalysts and alloy catalysts. Precious metals (such as palladium, platinum, ruthenium, rhodium, etc.) have empty d-electron orbitals, which are easy to be adsorbed with reactive species with moderate strength and promote the activation of reactive species with high catalytic activity. Palladium, rhodium, ruthenium, rhenium and other metal catalysts have been applied to the study of resin hydrogenation modification, in which palladium-based catalysts possess excellent hydrogen activation and dissociation ability, which gives them a significant advantage in resin hydrogenation activity. Although palladium-based catalysts are superior in hydrogenation performance, they are expensive and susceptible to deactivation by toxic impurities such as sulfides and chlorides in the resin, limiting their application in large-scale production, and the development of inexpensive and stable hydrogenation catalysts has become an urgent problem in the field of resin hydrogenation. Non-precious metal catalysts with excellent hydrogenation performance, abundant resources and low cost show promising development prospects. Among them, nickel-based catalysts are slightly inferior to palladium-based catalysts in terms of hydrogen activation and dissociation ability, but their low cost and good anti-poisoning ability have made nickel as the active metal component of industrialised resin hydrogenation catalysts a common choice, and a high content of nickel is loaded on the carrier to enhance the apparent hydrogenation activity of the catalysts. In order to combine the advantages of different active metals, researchers have also endeavoured to develop alloy catalysts that combine hydrogenation activity and stability through intermetallic interactions. Alloy catalysts have improved the hydrogenation activity and stability of the catalysts to a certain extent, but they still suffer from the problems of complicated preparation process and insufficient research on active sites.
In terms of the reaction system, petroleum resin, as an oligomer generated from the polymerisation of petroleum cracking to ethylene by-product, has a large relative molecular mass and molecular volume. For catalysts with tiny pore structure, it may be difficult for resin molecules to contact the surface active sites inside the catalyst pores for adsorption activation through intra-pore diffusion, so it is particularly important to improve the accessibility of active components to resin molecules to promote hydrogenation reactions. Secondly, the petroleum resin feedstock contains a high number of impurities, and the sulphur and halogen poisoning resistance as well as the sintering resistance of the metal catalysts are prerequisites for improving the stability and realising industrial applications. Most of the researchers based on the above points on the requirements of resin hydrogenation catalysts, around one or more of the catalysts to innovate, the following is a review of resin hydrogenation catalysts to highlight the dynamics of the research.
2.1 Dispersion of Metal Components
Early non-precious metal catalysts used in resin hydrogenation systems were mostly Raney nickel catalysts or nickel-based catalysts loaded on diatomaceous earth and alumina, which generally suffered from low hydrogenation efficiency, poor catalyst stability, and high product unsaturation. High loading, high-temperature thermal reduction and harsh reaction conditions lead to large nickel particle size, easy agglomeration and poor dispersion, which are the main reasons for the above problems. In order to improve the structural stability of resin hydrogenation catalysts and the dispersion of metal components, researchers usually use methods such as adding dispersants or metal additives during the catalyst preparation process to improve the dispersion and stability of the active components, and to increase the number of active sites and their hydrogenation performance.
The addition of chelating agents, dispersants or additives during the catalyst preparation process can usually improve the dispersion of the active components and enhance the hydrogenation performance of the catalyst. CNOOC Tianjin Research and Design Institute of Chemical Industry published a method for the preparation of a nickel-based catalyst with alumina as the carrier, PVC and citric acid as surfactants, zirconium and magnesium as metal additives, and a nickel mass fraction of 40% to 60%, which achieved a hydrogenation rate of 98.7% of C5 petroleum resins under the conditions of 260°C and 10 MPa. Li Yuefeng et al. investigated the effect of zinc and cobalt metal additives (mass fraction 0.1%~0.5%) on the performance of activated carbon loaded nickel (mass fraction 3%~8%) catalysts in the hydrogenation reaction of C5 petroleum resins, and found that the hydrogenation rate was increased from 30.87% to 94.25% compared with that of the catalysts without metal additives. Ji Jing et al. of China Petrochemical Company published a magnesium oxide and copper oxide additive modified (alumina-titanium oxide composite carrier) loaded nickel-based catalyst, and the hydrogenation rate of C5 petroleum resin reached 96.2% at a lower reaction temperature. BASF Corporation (USA) also announced a series of Co-Ni/SiO2-Al2O3 catalysts prepared by co-precipitation method with alumina and silicon oxide as the carriers and nickel and cobalt as the main active components for the resin hydrogenation reaction, and found that the hydrogenation activity could be increased by 70% when cobalt with a mass fraction of 0.3% was doped in the catalyst. The hydrogenation performance of the catalyst is closely related to the dispersion of the metal active sites, and the addition of metal additives not only prevents the agglomeration of nickel particles from increasing and maintains the stability of the catalyst's microscopic morphology, but also affects the hydrogenation performance of the catalyst by changing the electronic structure of the active sites through the interaction of metal additives.
Chelating agents can form stable complexes with metal ions, effectively inhibit the aggregation of metal particles, and significantly affect the dispersion and size of metal particles and their hydrogenation activity. Chen Xiaopeng's group conducted a series of studies on chelating agents to promote the dispersion and distribution of metal active components by using catalytic cracking catalyst residue as a carrier loaded with nickel. The team used citric acid and β-cyclodextrin as chelating agents to form chelates with nickel to prevent the agglomeration of nickel particles, improve the dispersion of nickel particles, and enhance the interaction between nickel active sites and carriers, respectively, during the catalyst preparation process. The addition of chelating agent increased the hydrogenation rate of the catalyst on C9 petroleum resin from 54.9% and 45.1% to 91.2% and 92.7%, respectively (Table 1), which significantly enhanced the hydrogenation activity of the catalyst.
Table 1 shows that the dispersing additives enhanced the dispersion of metal particles and catalytic hydrogenation activity
The dispersant of polymer compounds (such as polyethylene glycol, polyoxyethylene ether, polysorbate) can have affinity interaction with the particle surface, and by virtue of its macromolecular spatial site-blocking effect, it can effectively prevent the particle agglomeration and improve the degree of particle dispersion. Chen Xiaopeng's group used waste FCC catalyst residue as a carrier and added dispersant pyrrolidone or polyethylene glycol in the process of nickel impregnation. Pyrrolidone and polyethylene glycol have strong interaction with the carrier and form a competitive anchoring relationship with nickel nanoparticles, which promotes dispersion of nickel particles in the carrier, and thus improves the resin hydrotreating activity of the catalyst. Table 1 summarises the changes of dispersive additives on the particle size/dispersity of metal particles, and the addition of chelates such as β-cyclodextrin, pyrrolidone, and polyethylene glycol during the catalyst preparation process can all effectively improve the dispersity of the metal particles, and at the same time, there is a significant positive correlation between the dispersity of metal particles and the hydrogenation rate of the catalyst on petroleum resins. It can be seen that the modulation of the structure of the active metal components, such as the addition of chelating agents, dispersants and metal salt precursors to form complexes during the catalyst synthesis process can effectively inhibit the aggregation of metal particles and improve the dispersion of metal components. In addition, metal additives can also inhibit active metal agglomeration through intermetallic interaction and physical barrier. The highly dispersed metal components can provide a large number of active sites to efficiently adsorb and activate the reactant molecules and promote the hydrogenation reaction.
2.2Diffusion and adsorption of resin molecules
The diffusion of resin molecules into the active site area on the catalyst surface within the pore channel has a significant spatial site resistance effect. If the catalyst pore diameter is small, the resin molecules with a larger molecular volume are easier to contact the active sites on the catalyst surface and more difficult to contact the active sites inside the pore channel (Fig. 4), which leads to an inefficient utilisation of a large number of active sites. How to make the resin contact the active sites smoothly for effective adsorption activation is another key issue. The methods of constructing large-pore or open-pore carrier structure and controlling the distribution of active components on the outer surface of catalyst can effectively reduce the diffusion difficulty of resin molecules and enhance the adsorption capacity. Li Xiaonian's group at Zhejiang University of Technology proposed the strategy of increasing the pore size of the carrier to reduce the spatial site resistance, and investigated the influence of the average pore size of the carrier on Pd/γ-Al2O3 on the hydrogenation activity of C9 petroleum resin. They found that the resin molecules can enter into the carrier pore structure only when the catalyst pore diameter is large enough. They prepared three kinds of γ-Al2O3 carrier-loaded Pd catalysts with different pore diameters for the hydrogenation reaction of the resin, and found that there was an obvious positive correlation between the hydrogenation activity of the catalysts and carrier pore diameters, which confirms the important influence of pore size on the hydrogenation activity.
Figure 4 shows the schematic diagram of the diffusion of petroleum resin within the pore structure of catalysts
Starting from the distribution of metal active components, Chen Xiaopeng's group designed an eggshell-type nickel-based catalyst loaded with FCC catalyst residue, and they used n-heptane to soak the carrier to change its surface properties, which induced the nickel particles to be dispersed on the surface of the carrier, and the resin molecules were more likely to have access to the nickel sites. The distribution of nickel active sites was verified using ion beam cutting of the catalysts and scanning electron microscopy-energy dispersive X-ray spectroscopy (SEM-EDX) characterisation. For the eggshell catalysts, stronger nickel signals were revealed at the edges of the carriers, indicating that the nickel was mainly loaded on the surface of the catalysts [Fig. 5(a), (b)], and this construction of the surface active layer effectively reduced the diffusion distance required for the reaction of the resin molecules. Compared with the catalyst prepared by the common impregnation method, the hydrogenation rate of the resin was enhanced from 55.6% to 96.4%, and the catalyst had relatively good stability.
Figure 5 shows the distribution of active components in eggshell catalysts.
Carrier morphology engineering is an effective strategy to regulate the distribution state of active components, which plays a guiding role in the design of resin hydrogenation catalysts. Yuan Pei's group at Fuzhou University has made a unique design of catalyst morphology. They successfully constructed a cross-derived flower-like catalyst structure by preparing layered bimetallic hydroxide NiAl-LDH precursors by urea hydrolysis and synthesising nickel-copper silicate precursors on silica nanosheets, and then embedding the nanosheets into spherical silica surfaces. The active metal anchored on the "petal" surface, which is easy to contact with the resin molecules, not only promotes the exposure of more metal sites, but also facilitates the diffusion of the resin polymer molecules and their interactions with the metal sites.Wei et al. designed a nickel-loaded carbon nanotube catalyst in which the active metal is distributed on the outer surface of the carbon nanotubes, which is conducive to the contact of the resin molecules with the active component, achieving the desired effect of the cross-derivatisation. A similar effect was achieved by mutual contact with the active component.
In summary, for the non-homogeneous catalytic hydrogenation reaction of a class of macromolecular polymers including petroleum resins, it has become a consensus that the reaction is affected by internal diffusion, and the traditional methods usually use non-loaded and highly loaded metal catalysts to provide more active sites on the outer surface to enhance the adsorption and activation of resin molecules, but the active components on the inner surface of the catalyst pores are under-utilised. By constructing macroporous and open pore structures, regulating the distribution of active sites on the outer surface and unique carrier morphology, an effective technological approach is provided for the efficient adsorption of resin molecules on the active sites and the improvement of the utilisation efficiency of the active components, which reduces the amount of activated metal used and improves the technological and economic benefits.
2.3Electronic Role
The electronic structure of the metal has correlation with its catalytic performance, and the activity of the catalyst can be regulated by adjusting the electronic configuration of the metal catalyst and changing the adsorption strength of the species. The interaction between catalyst components is one of the important means to modulate the electronic properties of metal particles. In the resin hydrogenation catalytic system, researchers have modulated the electronic structure of catalysts and improved the catalyst performance by doping with heteroatoms, changing the nature of carriers, and constructing alloys.
Nickel hydrogenation activity is relatively weak, and usually requires high-temperature and high-pressure reaction conditions above 220 °C and 6~9 MPa. The harsh reaction conditions lead to chain-breaking degradation of the resin, which reduces the softening point of the resin to varying degrees and affects the quality of the resin. Therefore, it is of great significance to enhance the hydrogenation activity of nickel sites and achieve mild reaction conditions to improve the quality of the resin.Wu et al. prepared a nitrogen-doped carbon nanorods-loaded nickel catalyst with the formation of interactions between nitrogen and nickel, and appropriately increasing the roasting temperature could enhance the degree of Ni-N interaction and the hydrogenation activity of the catalyst, and the optimal hydrogenation rate of 96% was achieved at a roasting temperature of 400 °C [Fig. 6(a) ~ (d)]. (d)]. In addition, the catalytic effect of the nitrogen-doped catalyst reached a high level at the reaction temperature of 150 °C, and further increasing the temperature had little effect on the hydrogenation effect, which indicated that the catalyst already possessed a strong ability to dissociate hydrogen under the condition of 150 °C, and the reaction temperature was substantially reduced compared with that of the conventional nickel-based catalyst. Density Functional Theory (DFT) calculations showed that nickel on nitrogen-doped carbon has higher electron cloud density and lower adsorption energy when adsorbing resin molecules, indicating that nickel in the electron-rich state binds activated resin molecules more easily [Fig. 6(e), (f)]. Based on experiments and theoretical calculations, they proposed the resin hydrogenation reaction mechanism that electron-rich nickel injects electrons into the antibonding orbitals of hydrogen molecules, which promotes the dissociation of hydrogen. It can be concluded that the higher the charge density around the active site, the more favourable the hydrogenation reaction is.
Advances in Hydrogenation Catalysts for Petroleum Resins(3)

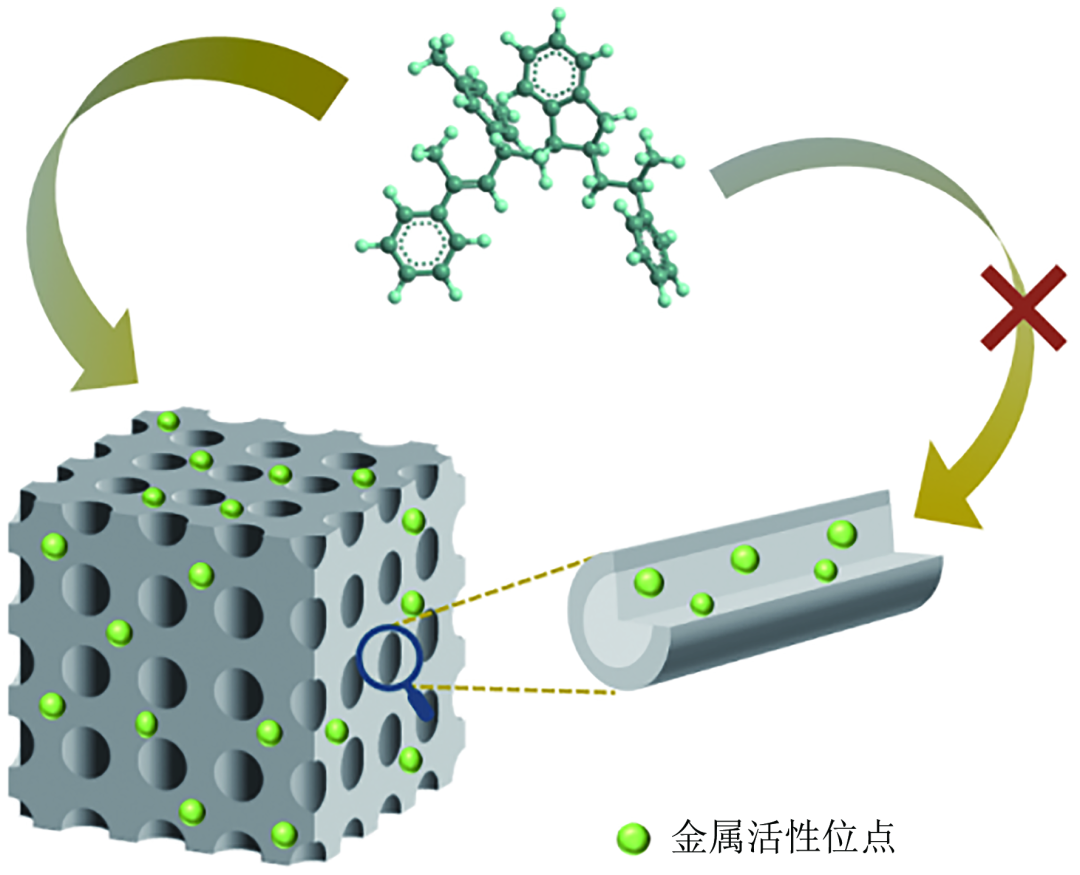
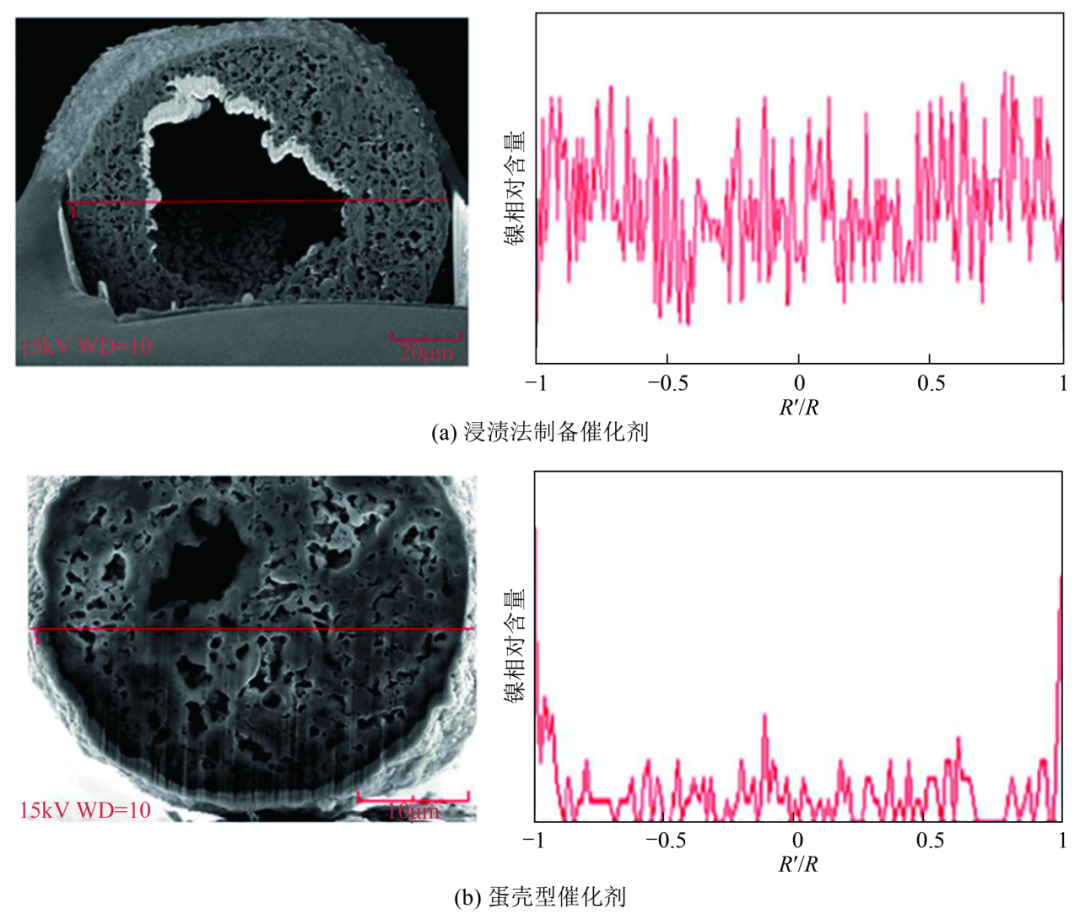
You must be logged in to post a review.
Reviews
There are no reviews yet.