Figure 6 shows the Ni-CQDs/NCNs catalyst characterisation and activity
Subsequently, Wei et al. further investigated on the idea of constructing Ni-N active sites, and they prepared nickel-based catalysts loaded on nitrogen-doped carbon nanorods by pyrolysis. The nickel was loaded on the defective sites generated by nitrogen doping using the impregnation method, and the nickel particles anchored on the defective sites had excellent anti-agglomeration ability during the reaction process and the active sites on the outer surface were more likely to interact with the unsaturated double bonds of the resin molecules, which significantly increased the catalytic activity and lowered the reaction temperature, and the hydrogenation rate of the resin was as high as 95.5% under the conditions of low temperature and low pressure (Table 2). Up to this point, there are sufficient research results to show that nitrogen as an electron-donating group can be used to achieve the resin hydrogenation reaction under low-temperature conditions, which is of great significance for the research and development of non-precious metal catalysts for resin hydrogenation.
In addition to the use of nitrogen as an electron-donating group, many researchers have devoted themselves to the study of the effect of charge transfer between alloys on the active sites, and to investigate whether metals with electron-donating ability have similar roles as nitrogen groups. Chen Xiaopeng's group prepared a Ni-Mo bimetallic catalyst loaded on carbon nanorods. They found by H2-programmed temperature-raising reduction (TPR), X-ray photoelectron spectroscopy (XPS), and X-ray diffraction (XRD) characterisation that the addition of Mo would put Ni in an electron-rich state to enhance the hydrogenation activity of the active site, and also enhance the interaction between Ni and the carrier to improve the dispersion of the Ni particles. The Ni-Mo/CNTs catalysts were used in the hydrogenation reaction of C5 petroleum resin, and a hydrogenation rate of 94.8% could be achieved, which is a great improvement in activity and stability compared with that of Ni/CNTs.
Yuan Pei's group published a method for the preparation of hollow nanorods catalysts with SiO2 as the carrier, Ni as the main active metal, and Cu/Co/Mg as the metal additives, in which the catalyst with metal Cu as the additive had the best performance in the hydrogenation test, with the bromine value of the resin decreasing from 28.6 gBr/100 g to 1.05 gBr/100 g, along with the smallest decrease of the softening point. Subsequently, the group conducted a modification study of NiCu/SiO2 catalysts based on NiCu bimetallic active sites. They synthesised nickel-copper silicate precursors on silica nanosheets, nickel-copper silicate was reduced to form CuNi nanoparticles, and the nanosheets were then embedded in the surface of spherical silicon dioxide to form cross-derivatised floral-structured NiCu/SiO2 catalysts.Binding energies of the Cu 2p and Ni 2p orbitals were shifted in the XPS spectrum, which indicated the formation of CuNi alloying sites [Fig. 7(a)~(c)]. Compared with the NiCu alloy catalysts and monometallic Ni catalysts prepared by impregnation method, the formation of CuNi alloys in the flower-like structured NiCu/SiO2 enhanced the catalytic activity, confirming the effect of intermetallic charge transfer on the hydrogenation activity of the catalysts.
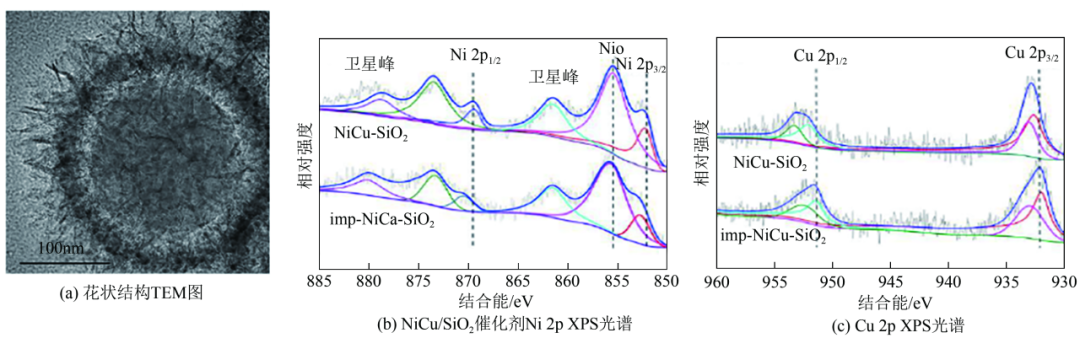
Figure 7 shows the NiCu/SiO2 catalyst characterisation
Alloy catalysts can change the structure and surface interface properties of catalysts through intermetallic interactions, and the strength of intermetallic interactions can have a crucial effect on the catalytic effect. In order to investigate the effect of intermetallic interactions on the hydrogenation activity of the catalysts, Bai et al. prepared Cu-Ni-Al hydrotalcites (HTLCs) precursors with different Cu/Ni ratios by co-precipitation, and then obtained a series of highly dispersed Cux-Niy-Al2O3 catalysts with strong intermetallic interactions by thermal reduction.The results of XRD, TEM and other characterizations proved that the hydrotalcites precursors successfully increased the Cu/Ni ratio, and the hydrotalcites precursors were highly dispersed. derived catalysts successfully improved the dispersion of the active sites of Cu-Ni alloys, and the particle size of the metal nanoparticles was only 6-7 nm, which had a significant advantage over the metal nanoparticles of about 20 nm of the Cu1-Ni3/Al2O3 catalysts prepared by impregnation. In addition, the addition of copper could promote the reduction of nickel species and inhibit the generation of NiAl2O4 structure, which shifted the reduction peak of nickel to low temperature, corroborating that strong Cu-Ni interactions occurred in the Cux-Ni3-Al2O3 catalyst. The hydrogenation performance results showed that the Cu1-Ni3-Al2O3 catalyst exhibited the best hydrogenation activity towards the DCPD resin and resin monomer, with a 98% hydrogenation rate of the resin under the reaction conditions of 250 °C and 8 MPa (Table 2), which is a substantial increase in the hydrogenation performance of the catalysts compared with the catalysts prepared by the impregnation method and the mechanical mixing method, which confirms the important Cu-Ni synergistic effect on catalytic activity Effect of copper-nickel synergism on catalytic activity.
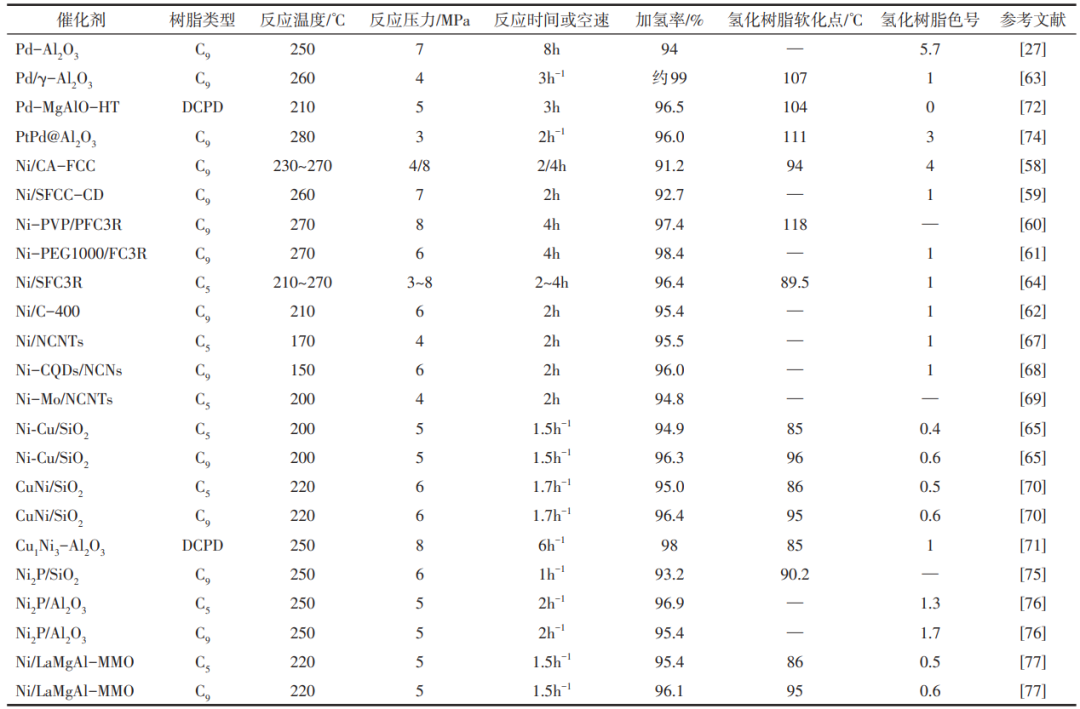
In summary, the performance of the catalyst can be significantly affected by modulating the electronic properties of the nickel active site. When the nickel active site is in the electron-rich state, the dissociation ability of hydrogen will be increased, which is manifested as the enhanced hydrogenation ability of petroleum resin. When the nickel active site is in the electron-deficient state, the binding ability with the sulfur and halogen atoms in the petroleum resin will be decreased, which is manifested as an increase in the anti-poisoning ability of the catalyst. As the modulation of metal electronic structure can make significant changes in the performance of catalysts, which is of great significance for the improvement of catalysts, the study of modulating metal valence state has gradually become a hot spot in recent years. However, the calculation of the electronic structure of some magnetic active metals, such as nickel and cobalt, is still difficult and not thorough enough, and the theoretical calculation process of polymer macromolecule adsorption and reaction is also difficult to carry out. Therefore, this part of research still needs attention and finding solutions at present.
2.4
Stability
Stability is one of the important indicators of catalyst performance, and in the field of resin hydrogenation, effective control of catalyst poisoning deactivation, metal active site leaching loss and sintering deactivation is a prerequisite for the industrial application of catalysts. Existing literature usually adopts the enhancement of the interaction between metal nanoparticles and carriers to solve the problem of easy leaching of metal components, and the construction of amorphous alloys (e.g. Ni2P) active sites to reduce the binding capacity of nickel with sulfur and halogen elements in the reaction system, so as to prevent the poisoning and deactivation of metal active sites.
Palladium as a noble metal catalyst shows excellent hydrogenation activity, but the palladium nanoparticles are difficult to be stably loaded on the carrier, and it is easy to leach out and lose the active sites, so how to make the palladium active sites effectively stabilised on the surface of the carrier is crucial to enhance the stability and lifetime of the catalyst.Bai et al. prepared Pd-Mg-Al hydrotalc-like precursors by co-precipitation, and a large number of exchangeable hydrotalc-like hydrotalc-like layers are distributed in the layered structure. The interlayer anions, and the positively charged palladium ions can be tightly attached to the laminates, and the Pd-MgAlO-HT catalysts with good dispersion and tight binding of the palladium active sites to the carriers were obtained after roasting and reduction. The structural characterisation results showed that the average particle size of Pd particles in the Pd-MgAlO-HT catalyst was only 2.25 nm, indicating that the strong metal-carrier interaction effectively prevented the agglomeration of metal nanoparticles. The catalyst was used in the hydrogenation reaction of DCPD resin with a high hydrogenation rate of 96.5%, and the hydrogenation activity of the catalyst only decreased by 3.57% after 5 cycles of the reaction, which resulted in a significant stability enhancement compared with the Pd/MgAlO-IM catalyst prepared by the impregnation method [Fig. 8(a), (b)]. By deriving palladium-based catalysts with strong metal-carrier interactions through a hydrotalcite-like structure, this method successfully improves the dispersion and stability of palladium particles, and solves the problem of easy leaching of precious metals to some extent.
Figure 8 shows the cyclic stability and structural characterisation of palladium-based catalysts in the hydrogenation reaction of DCPD resin.
The deactivation of metal catalysts by combining with sulfur and halogen elements is another key factor limiting the service life of catalysts, especially for precious metal catalysts, if the problem of easy poisoning and deactivation of catalysts cannot be solved, the production cost will be greatly increased, which greatly restricts the application of catalysts in industrial production. In order to solve this problem, Sued Chemie Catalysts published a Pd and Pt bimetallic catalyst loaded on alumina prepared by impregnation method and applied it to the HDS reaction of high sulphur resins, and they found that the catalyst has the best hydrotreating activity and stability when the mass fraction of Pd in the catalyst is 0.6% and that of Pt is 0.2%, and that the catalyst has the best hydrotreating activity and stability when the mass fraction of Pd in the catalyst is 0.2%. Further increase in the content of precious metals in the catalyst will cause the activity and stability of the catalyst to decrease. Liang Changhai et al. of Dalian University of Technology published a sulfur-resistant eggshell-type noble metal alloy catalyst in 2021, which loaded Pd with one or two or more of Ir, Re, Pt, Ru, Au, and Ag on Al2O3, SiO2, TiO2, SiO2Al2O3, or Al2O3TiO2, and used it for hydrodesulfurisation of petroleum resins to improve the defect of the Pd catalysts that are prone to poisoning. . The researchers found that PtPd@Al2O3, PtPd@SiO2Al2O3, and PtPd@Al2O3TiO2 catalysts have significantly better HDS capability by screening the hydrotreating activity of a series of catalysts (Fig. 9), and the PtPd@Al2O3 catalysts can reduce the sulphur content of resins from 480 μg/g to 23 μg/g under the test conditions of 260 °C and 3 MPa. The PtPd@Al2O3 catalyst can reduce the sulfur content in the resin from 480 μg/g to 23 μg/g at 260 °C and 3 MPa, and the catalyst is still stable after 1000 h of reaction, which indicates that the construction of the alloy active sites can effectively improve the poisoning resistance of precious metal catalysts and enhance the stability of catalysts.
Figure 9 shows the resin hydrogenation activity of different alloy catalysts
Compared with noble metal catalysts, non-precious metal catalysts are more prone to deactivation by poisoning in combination with sulfur, halogen and other elements in resin, which has a significant impact on the application of non-precious metal catalysts in industrial production. The construction of Ni-P active sites is one of the ideas for researchers to solve the poisoning and deactivation of Ni. Jiang et al. prepared Ni2P/SiO2 catalysts with 10% nickel loading by dissolving diammonium hydroxide phosphate and nickel nitrate with nitric acid to obtain a mixed solution of Ni and P elements, and then using the impregnation method. The petroleum resin hydrogenation reaction was carried out under the test conditions of 250 °C, 6 MPa, and liquid-time space velocity (LHSV) of 1.0 h-1, and the catalysts still possessed stable activity after 300 h of reaction, with a hydrogenation rate of 93% (Table 2). The construction of Ni2P active sites allowed the formation of more stable and smaller particle size spherical nanoparticles with higher active site exposure. Meanwhile, the special crystalline phase formed by Ni2P resulted in the increase of d-band holes, which showed similar properties to those of noble metals, and these factors together resulted in the excellent resin hydrogenation activity of Ni2P/SiO2 catalysts [Figure 10(a)~(c)].
Figure 10 shows the characterisation of nickel-based catalysts
The researchers found that during the preparation of nickel phosphide catalysts, if traditional Al2O3 is used as a carrier, it is easy to form inert AlPO4 coating the catalyst surface, which makes it difficult to obtain Ni-P/Al2O3 catalysts by impregnation method and thermal reduction method. In order to make better use of alumina, a mature and resourceful carrier, Yuan Pei et al. from Fuzhou University published a patent for the preparation of loaded nickel phosphide catalysts using urea hydrolysis (generation of hydrotalcite-like precursors through the reaction of carbonate and hydroxide produced by urea hydrolysis with metal ions). They obtained Ni2P/Al2O3 catalysts by mixing carbonate-inserted NiAl binary hydrotalcite precursors with different phosphorus sources (red phosphorus, ammonium hypophosphite, and phosphite pressed, etc.) in a reducing atmosphere at high temperature. The resulting catalysts were characterised by XRD without the characteristic diffraction peaks of AlPO4, in which the Ni2P/Al2O3 produced by using red phosphorus as the phosphorus source could reduce the bromine value of C5 petroleum resin from 16.4 gBr/100 g to 0.51 gBr/100 g (Table 2), which was a clear advantage compared with that of the catalyst prepared by the impregnation method. They further investigated the Ni2P/Al2O3 catalyst prepared with red phosphorus as the phosphorus source, and found that its hydrogenation performance was greatly related to the content of Niδ+, and the presence of Niδ+ and Pδ- indicated that there was an electron-transferring behaviour from Ni to P in the active site of Ni2P, and the electron-deficient Ni had a great role in improving the defects of the catalyst, which was easy to deactivate by combining with sulfur and halogens. Thereafter, the group prepared NiLaMgAl-LDHs precursors based on urea hydrolysis and obtained Ni/LaMgAl mixed metal oxide catalysts by thermal reduction, which achieved 95.4% and 96.1% hydrogenation of C5 and C9 petroleum resins, respectively, at 220 °C and 5 MPa (Table 2). They demonstrated by XRD, H2-TPR, and CO2-programmed temperature rise desorption (TPD) characterisations that the doping of La effectively increased the dispersion of Ni active sites, promoted the reduction of Ni, increased the number of basic sites, and inhibited the fracture of the resin carbon chain, which achieved the improvement of the quality of hydrogenated resins [Fig. 10(d)~(f)].
Overall, the metal active sites can be effectively anchored and active metal leaching can be effectively inhibited by enhancing the strength of the carrier's interaction with metal nanoparticles, such as the preparation of hydrotalcite-like and layered polymetallic hydroxide precursors. The construction of amorphous alloys and alloy catalysts, on the other hand, can reduce the binding ability of active metals with sulfur and halogen atoms by regulating the metal valence state, so as to achieve the purpose of improving catalyst stability and prolonging catalyst service life. However, at present, the catalyst stability research in the field of resin hydrogenation mainly focuses on solving the problems of active metal leaching and poisoning deactivation, while the existence of active metal agglomeration deactivation and resin molecule cleavage and carbon accumulation phenomenon during the reaction process have been less reported, and these problems still need to be paid attention to and solved in the practical application of catalysts.
3
Summary and Prospect
The molecular structure of petroleum resins is complex and diverse, and the chemical environments of carbon-carbon double bonds are different (e.g., straight chain, benzene ring, and pentane ring), and the degree of difficulty of hydrogenation reaction varies accordingly. The degree of hydrogenation saturation of the resin molecules will change their softening point, viscosity, chroma and other properties. The creation of highly selective hydrogenation catalysts to achieve the directional hydrogenation of the carbon-carbon double bonds and the controllable modulation of the properties of the hydrogenated resin is of great significance to the manufacture of high-quality resin products. Resin hydrogenation catalysts focus on loaded palladium-based catalysts, nickel-based catalysts and palladium and nickel-based alloy catalysts. Palladium-based catalysts have superior performance, require mild reaction conditions, and can effectively inhibit resin degradation side reactions. Nickel-based catalysts have the advantages of abundant resources and low price, but the catalytic hydrogenation activity is not as good as that of palladium-based catalysts. The resin hydrogenation performance can be significantly improved by constructing special morphology catalysts such as eggshell and flower catalysts, and amorphous nickel alloy catalysts (e.g. nickel nitride and nickel phosphide). After years of research and exploration, the development and industrial application of resin hydrogenation catalysts have made significant progress, but there is still room for improvement in catalyst stability and selective hydrogenation capacity.
(1) Petroleum resin is a complex raw material containing toxic substances such as sulfur, halogen impurities and heavy metals, which can easily poison and deactivate the active sites of the catalyst, thus affecting the activity and stability of the catalyst. Industrial production usually adopts a multi-stage hydrogenation process to desulfurise and dehalogenate the resin feedstock through hydrogenation pretreatment. The development of sulfur- and halogen-resistant catalysts to achieve a one-stage hydrogenation process is of great value for the industrial production of petroleum resin hydrogenation. Loaded sulphide catalysts have high resistance to poisoning, but generally have low hydrogenation activity. Sulfides show the characteristics of layered structure, and the hydrogenation activity is related to the number of layers and the edge site defects of the laminates, etc. Therefore, the design and development of single-layer dispersed, cluster-scale sulfide catalysts can be considered in the future work to create more active sites and improve the hydrogenation reaction performance.
(2) Petroleum resin, as a macromolecular polymer, has the possibility of polymerisation or cracking reactions during hydrogenation, and the accumulation of polymers or carbon on the catalyst surface can easily cause structural damage such as pore blockage or pore collapse, resulting in catalyst deactivation. Existing studies have paid little attention to the deactivation mechanism of resin hydrogenation catalysts and the regeneration process of catalysts. Future studies can focus on the deactivation mechanism and regeneration methods, which are of great significance in guiding the industrial application of catalysts.
(3) Non-precious metal nickel-based catalysts usually require high-temperature and high-pressure reaction conditions, and the harsh reaction process consumes a lot of energy and leads to irreversible degradation of resin molecules, which affects the quality of the resin. To address this point, the charge density around the active sites can be increased by constructing Ni-N active sites and bimetallic active sites, so that they have the ability to dissociate hydrogen at low temperatures, which can reduce the reaction temperature and realise the hydrogenation reaction of petroleum resins under mild conditions. However, the research on the active sites and reaction mechanism of alloy catalysts is still insufficient, especially the in-situ characterisation of the reaction is almost unreported. In the future, the research can try to develop the in-situ characterisation technology of petroleum resin hydrogenation reaction to deepen the knowledge and understanding of the reaction mechanism and to guide the rational design and development of high-performance resin hydrogenation catalysts.
Advances in Hydrogenation Catalysts for Petroleum Resins(1)
Reviews
There are no reviews yet.