Refined C5 petroleum resin for tire rubber compounding
Refined C5 petroleum resin for tire rubber compounding
If you need COA or TDS, please fill in your contact information in the form below, we will usually contact you within 24 hours. You could also email me info@longchangchemical.com during working hours ( 8:30 am to 6:00 pm UTC+8 Mon.~Sat. )
1. Has excellent viscosity
Other uses:
High-end hydrogenated petroleum resins are widely used and the market demand is increasing year by year, how to achieve efficient production of high-quality hydrogenated petroleum resins is the focus of research in this field. The production of high quality hydrogenated petroleum resins is mainly based on catalytic hydrogenation technology, and the development of efficient and stable hydrogenation catalysts is a key technical link. This paper focuses on the low hydrogenation efficiency of catalysts, the difficulties in diffusion and adsorption of resin molecules, and the harsh conditions of the hydrogenation reaction, and summarises the research results of researchers in recent years on the composition of the metal active components, the geometrical and electronic structures of catalysts, and the design of carrier morphology and pore structure in order to solve the above difficulties. It is proposed that the dispersion of metal active sites, site distribution, valence modulation and synergistic effect between composite metals are the keys to modulate the performance of catalysts. Meanwhile, the current design of active sites, reaction mechanism, catalyst deactivation and regeneration mechanism of petroleum resin hydrogenation catalysts are summarised and the future development of catalysts is expected.
Petroleum resin is a low molecular weight (200~3000) thermoplastic polymer made from the C5~C9 fractions of petroleum cracking by-products through polymerisation reaction and other processes, which has good water resistance, acid and alkali resistance, and is widely used in the fields of coatings, rubber auxiliaries, paper additives, printing inks and adhesives. However, untreated petroleum resins contain a complex variety of unsaturated groups (e.g. alkenyl, aryl) as well as impurities (e.g. halides, sulphides, etc.), which directly affect the properties of the resins (light and heat stability, softening point, viscosity, chromaticity, etc.). The chromaticity of the resin is strongly related to the presence of conjugated unsaturated bonds in the polymer, and in particular to the indene structure of the resin, while the odour emitted by the resin when heated is related to sulphides. The defects of unrefined petroleum resins make it difficult to apply them directly to the production of their downstream high value-added products. Industrial production usually takes the method of modification to improve the quality of the resin, and hydrogenation is the most direct and effective method of petroleum resin modification. Catalytic hydrogenation can effectively hydrogenate the unsaturated double bonds in the molecular structure of the resin, remove heteroatoms such as sulphur and halogens, and improve the stability, viscosity, transparency and oxidation resistance of the resin. In view of the complexity and variety of petroleum resin types and molecular structures, it is the goal of current scientific research to develop highly active, highly selective and long-life hydrogenation catalysts, and to orientate the conversion of unsaturated bonds, carbon-sulfur bonds and other functional groups in petroleum resins under suitable process conditions, so as to obtain high-end petroleum resins that can be applied to high value-added products, such as graphite, adhesives, and disposable sanitary products.
In recent years, China's market demand for high-quality hydrogenated petroleum resins has been growing year by year, but China's petroleum resin hydrogenation industry started late compared with developed countries, and both the production equipment and commercial catalysts are not mature enough. There are problems such as low saturation, dark colour, low softening point, etc. This is mainly due to the existing catalysts have insufficient hydrogenation performance, poor stability, hydrogenation reaction conditions are more demanding and other defects, which seriously restricts the production of high-quality hydrogenated petroleum resins. Currently, the catalysts used in the hydrogenation of petroleum resins mainly include: noble metal catalysts, such as Pd/Al2O3; non-precious metal catalysts, such as Raney nickel, Ni/SiO2, etc.; and alloy catalysts, such as NiCu/SiO2, etc. The above three types of catalysts are very similar in structure, stability and performance. The above three types of catalysts are different in terms of structure, surface interface properties and hydrogenation performance: noble metal catalysts have excellent hydrogenation performance, but they are easily affected by the high content of sulphur and halogen in petroleum resins, which makes it difficult to control the production cost; non-precious metal catalysts are rich in resources and have excellent hydrogenation activity, but they require harsh hydrogenation conditions, which is not conducive to the production of resins with a high softening point; and the alloy catalysts have the following problems: difficult preparation, insufficient study of active sites, and insufficient research on the active sites. The alloy catalysts are difficult to prepare and the active sites are not sufficiently studied, which restricts their application in industrial production. In recent years, resin hydrogenation catalysts have made great progress in hydrogenation performance, stability and compound active site research, but there is a lack of corresponding review articles to summarise the recent research results. This paper will summarise the recent progress of research related to resin hydrogenation catalysts, and point out the shortcomings of the current research and the direction of future development.
In this review, the classification, application and modification methods of petroleum resins are briefly introduced, among which, the hydrogenation modification of petroleum resins is highlighted. Then, it elaborates the petroleum resin hydrogenation process and its characteristics, and introduces the typical two-stage fixed-bed hydrogenation reaction unit which is widely used in China at present. The research results on the development of petroleum resin hydrogenation catalysts in recent years are summarised, including the improvement of the dispersion of metal components by additives, the control of catalyst morphology, and the modification of metal active sites to enhance the hydrogenation performance of the catalysts. The effects of catalyst active site dispersion, active site distribution in the carrier, valence modulation of active metals, and synergistic effects between catalyst components on the hydrogenation performance of catalysts are discussed. Finally, a summary of the current problems in the field of resin catalytic hydrogenation, such as the lack of thorough and in-depth research on complex active sites, the lack of in-situ characterisation of catalysts, the lack of research on catalyst deactivation and regeneration mechanism, and the lack of theoretical calculation support for the adsorption of polymer molecules on active sites, is given, and an outlook is given on the development of resin hydrogenation catalysts in the future.
1
Petroleum Resin
1.1
Classification and application of petroleum resin
Petroleum resins are mainly divided into three categories: C5 petroleum resins, C9 petroleum resins and dicyclopentadiene resins (DCPD resins). There are differences in the structure and molecular weight of the three, and their applications are also focused. Among them, C5 petroleum resin is mainly made of aliphatic olefins (such as pentadiene, 2-methylbutene) and unsaturated alicyclic hydrocarbons (such as cyclopentene, cyclopentadiene) as the monomer polymerisation [Fig. 1(a)], with stable adhesive properties, high adhesive strength, high speed, and is used for viscosity builder, filler, additives, etc. to increase the viscosity of the main body.C9 petroleum resins are classified into catalytic polymerisation (cold polymerisation), hot polymerisation, and hot polymerisation (cold polymerisation). C9 petroleum resin according to the polymerization method can be divided into catalytic polymerization (cold polymerization), hot polymerization of petroleum resins, as well as initiated polymerization of petroleum resins, whose main components include olefins, cyclo-olefins, aromatic hydrocarbons, indene, etc. [Figure 1 (b)], because it does not contain or rarely contain polar groups, with excellent water resistance, acid and alkali resistance, in the field of coatings, rubber auxiliaries, paper additives, ink additives have important applications.DCPD resins are usually obtained by the bis(cyclopentadiene) polymerization at high temperature and high pressure, hydrogenated DCPD resins, which can be obtained by the polymerization of the resin, and the polymerisation of the resin. DCPD resins are usually obtained by polymerisation of dicyclopentadiene under high temperature and high pressure. Hydrogenated DCPD resins have the features of high softening point, good viscosity enhancement, excellent gloss index, etc., and they are usually used in the fields of rubber compounding and ink additives.
Figure 1 shows the main components of petroleum resins
1.2
Modification of petroleum resin
Unmodified petroleum resin has defects in stability, adhesion, colour, oxidation resistance, etc., and its practical application range and scale are limited, and its economic value is not high. Modified petroleum resin can improve its performance and quality, expand the scope of application, and better meet the application needs of different fields.
Petroleum resin modification methods mainly include chemical modification (the introduction of hydrocarbon modification, the introduction of polar group modification) and polymerisation product hydrogenation modification. Among them, the introduction of hydrocarbons can adjust the softening point and melt viscosity of the resin, and under the condition of excluding the influence of the polymerisation process, the softening point and melt viscosity of the product will increase with the increase of the amount of mono-olefin introduced. For C5 petroleum resin, by introducing mono-olefin and controlling the mass fraction of C5 (C5 fraction containing less unsaturated bonds and heteroatoms) at 68%~75%, petroleum resin with softening point and melt viscosity in the appropriate range can be produced. The introduction of polar groups can significantly improve the compatibility of the resin with other materials and enhance the performance of synthetic materials. For example, the introduction of maleic anhydride with a mass fraction of 8% into petroleum resin through polymerisation reaction at 200°C can achieve a high grafting rate of maleic anhydride, which not only raises the softening point of petroleum resin by 40°C, but also improves the adhesion of the resin by three times.
Catalytic hydrogenation is the simplest and most effective refining method in the modification of petroleum resins. Catalytic hydrogenation of resins using suitable catalysts can effectively restore the unsaturated carbon-carbon double bonds in the structural units of the resins and enhance the stability of the resins. Hydrogenation of petroleum resins can also reduce the content of halogens, sulphur and other heteroatoms and destroy the colour rendering units in the resin, improving its adhesion and colour and other qualities. However, the types and molecular structures of petroleum resins are complex and varied, and the chemical environments of the functional groups of the unsaturated carbon-carbon double bonds (e.g., benzene rings, aliphatic olefins) and the degree of difficulty of hydrogenation are not the same. Generally, hydrogenation reactions occur preferentially on olefinic double bonds, and as the reaction proceeds, benzene double bonds are also hydrogenated to varying degrees (Fig. 2). 2010, Sae-Ma et al. from Chulalongkorn University, Thailand, investigated the relationship between resin chromaticity and the degree of hydrogenation of unsaturated groups. By comparing the hydrogenation status of two petroleum resins containing aromatic and vinyl functional groups respectively, they found that for resins containing only aromatic unsaturated bonds, the colour of the resins became significantly lighter with the increase in the degree of hydrogenation of the aromatic groups, while for resins with a predominantly vinyl structure, the degree of hydrogenation of the unsaturated double bonds was basically independent of the change in the colour of the resins. Therefore, selective hydrogenation can achieve precise catalytic reduction of unsaturated carbon-carbon double bonds and elimination of impurities, modulate the degree of unsaturation and properties of petroleum resins, and meet the production requirements of different applications. At present, catalytic hydrogenation is the most researched and concerned direction in the field of petroleum resin modification. This paper focuses on the catalytic hydrogenation technology of petroleum resins and reviews the research progress of petroleum resin hydrogenation process and catalysts.
Figure 2 shows a schematic of the hydrogenation reaction of resin molecules
1.3
Petroleum resin hydrogenation process
Petroleum resin hydrogenation process is a gas-liquid-solid three-phase reaction. At present, the production process of hydrogenated petroleum resin is mainly divided into three types of hydrogenation processes: slurry bed, fixed bed and spraying, of which the more mature technology is slurry bed and fixed bed hydrogenation. According to the number of stages, the petroleum resin hydrogenation process can be generally categorised into one-stage hydrogenation and multi-stage hydrogenation technology. One-stage hydrogenation refers to the direct completion of the hydrogenation of unsaturated double bonds and the removal of sulfur and halogens and other heteroatoms in the petroleum resin during the hydrogenation reaction, without the need for a subsequent hydrogenation step. This process route has a high utilisation of equipment, but the catalyst performance requirements are relatively stringent, and it must be able to have the ability of deep hydrogenation of the resin and good stability. Multi-stage hydrogenation process generally consists of two stages: the first stage of low-pressure hydrogenation and the second stage of high-pressure hydrogenation, which has a long process flow and a large investment in equipment. However, the multi-stage hydrogenation process can hydrogenate different functional groups and impurities in the resin through segmented reactions, and suitable catalysts can be selected for the characteristics of each reaction process. In a two-stage hydrogenation plant, the first stage usually uses inexpensive non-precious metal catalysts for preliminary hydrogenation and desulfurisation and dehalogenation of the resin at low temperatures and pressures, and the second stage uses precious metal catalysts for in-depth hydrogenation of the resin at high temperatures and pressures.
A typical multi-stage fixed-bed hydrogenation process flow is shown in Figure 3. The petroleum resin feedstock and solvent are slurried and mixed in a high-temperature mixing device, and the petroleum resin solution is mixed with hydrogen and then entered into a one-stage hydrogenation reactor, and the hydrogenated material is cooled and separated, and hydrogen and hydrogen chloride and other gases are entered into a storage tank, and the hydrogenated petroleum resin solution is transferred to a heating furnace for preheating, and the deep hydrogenation is completed in the two-stage hydrogenation reactor, and the material is cooled and separated after the two-stage hydrogenation, and the separated petroleum resin solution The separated petroleum resin solution enters the stripping tower to separate the solvent and hydrogenated petroleum resin, and the solvent is recycled after recovery treatment. In actual industrial production, in order to achieve the efficient use of solvents, heat and other factors of production, usually in the process of adding more than one stripper tower, pumps and other separation and recycling devices. Because of the advantages of easy separation and continuous production, most of the production of hydrogenated petroleum resins in China adopts the multi-stage fixed-bed hydrogenation process.
Figure 3 shows the fixed-bed resin hydrogenation process flow diagram
1-Resin feedstock; 2-Solvent; 3-Heating and mixing device; 4-Hydrogen; 5-Stage one hydrogenation reactor; 6, 10-Hydrogen chloride, hydrogen sulphide, etc.; 7, 11 -separation unit; 8-heating unit; 9-second stage hydrogenation reactor; 12-vapour extraction tower; 13-resin product; 14-recovery of solvent; 15 -impurities; 16 - solvent recovery unit
Advances in Hydrogenation Catalysts for Petroleum Resins(2)
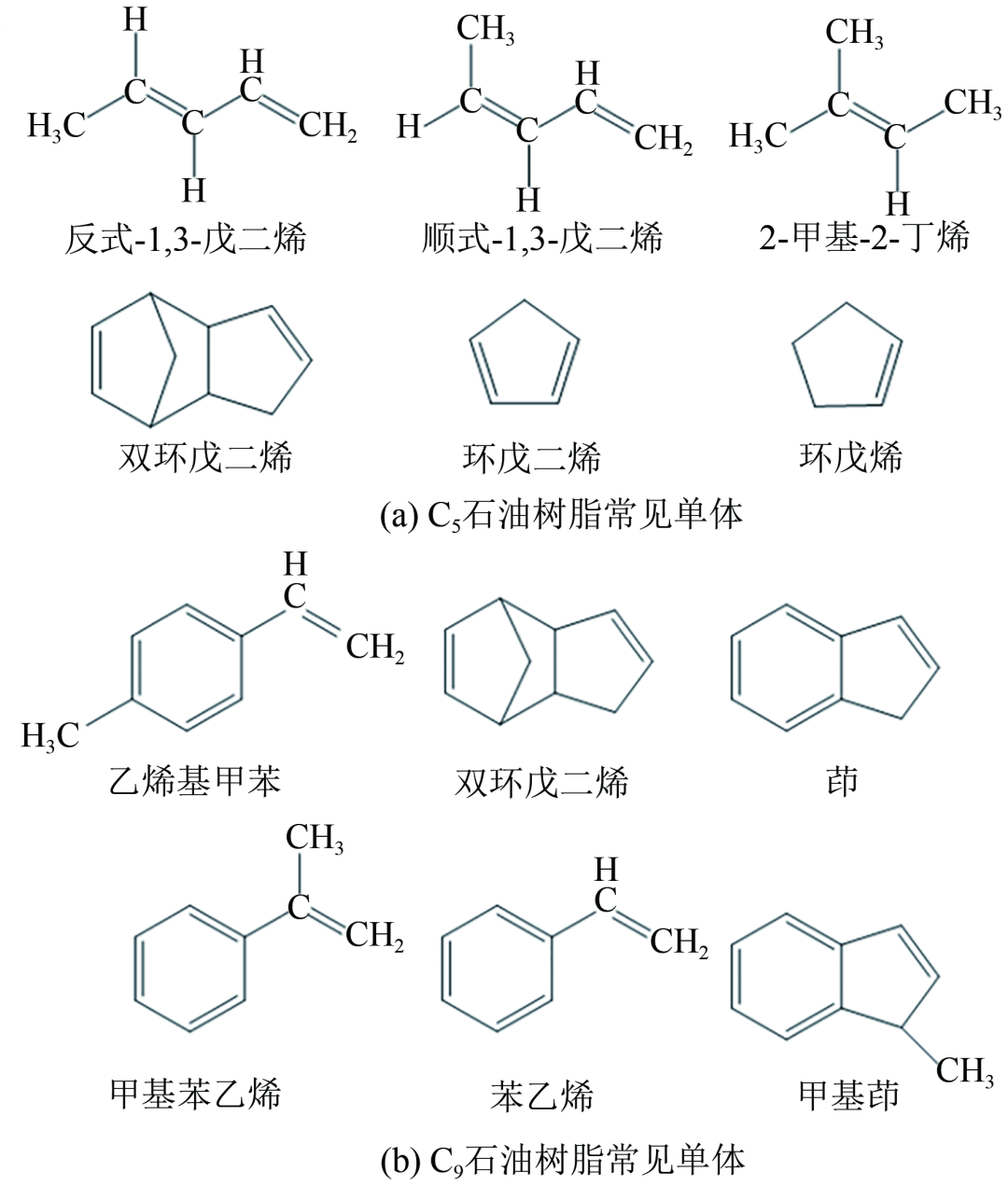
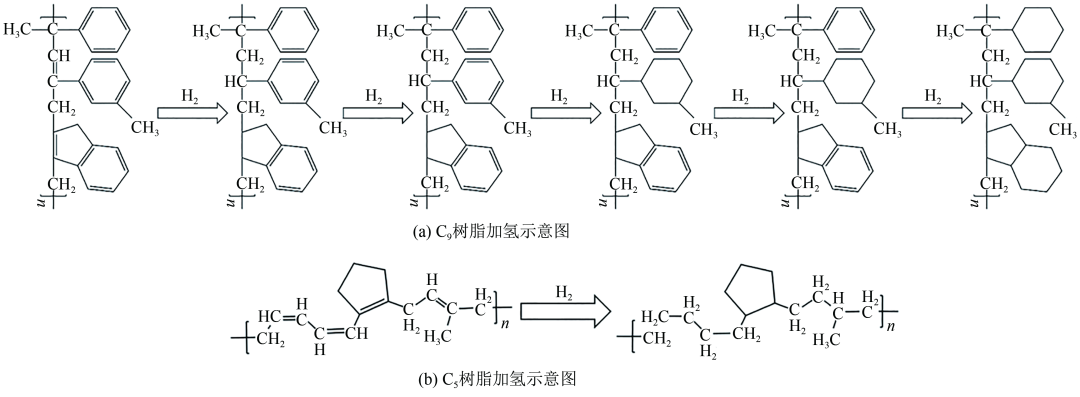
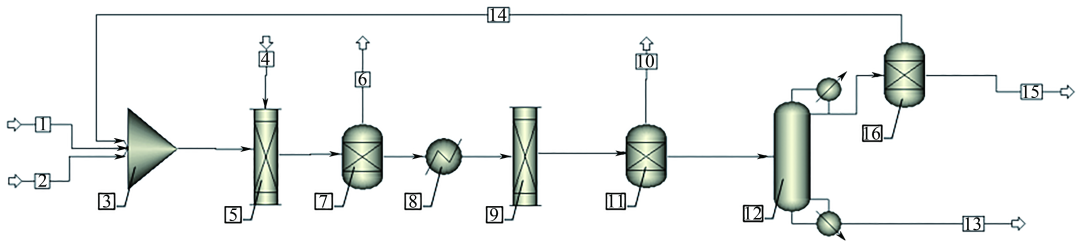
You must be logged in to post a review.
Reviews
There are no reviews yet.