Light curing bamboo wood coating
In today’s materials science and industrial applications of the bright starry sky, light-curing coatings like a dazzling star, is with its unique charm shining in many areas. The reason why light-curing coatings can win widespread favor, the root cause is that it is a set of rapid drying and curing, environmental protection and energy saving and many other advantages in one, just like an all-rounders, quickly in the various industries to emerge.
Looking back, the development of light-curing coatings has a clear vein. In the early years, it is mainly in the field of wood coatings to show their fists, for wooden products with a layer of protection and decoration both “coat”. And nearly twenty years time, can be called the golden period of development of light-curing coatings. With researchers in the efficient photoinitiators, active diluents and oligomers and other key areas of continuous attack, a series of breakthroughs such as the emergence of spring-like results. At the same time, keen insight into the market demand for enterprises and R & D team precision efforts to promote the UV curing technology to expand the boundaries of its application map can be steadily expanded.
At present, the light-curing coatings family is flourishing, covering light-curing bamboo coatings, paper coatings, plastic coatings and other categories, widely penetrated into all aspects of our life and production. From the daily life of bamboo and wood flooring, furniture, to industrial manufacturing of metal parts, electronic components, to the automotive field of body painting, and even decorative field of fabric printing and dyeing, there are light-curing coatings busy figure. Moreover, its appearance style has undergone a magnificent transformation, from the initial single high-gloss type, all the way to matte type, frosted type, metal flash type and other diversified styles to meet the increasingly diverse aesthetic needs of people. The coating method is even more blossoming, roller coating, scraping, spraying, etc., each showing their skills, adapting to different scenes and substrates.
Focusing on light-curing bamboo coatings, it is the “front-runner” in the light-curing coatings camp, not only considerable production, but also the first to start the industrialization journey. Dating back to the early 1960s, the German company Bayer took the lead and successfully developed the first generation of light-curing coatings — light-curing bamboo wood coatings, which made great achievements for the development of the industry. The advantages of this type of coating are significant, with outstanding coating performance, lightning fast curing, steady as a mountain in the application of equipment, pro-people processing costs, and more critically, extremely low or even zero emissions of organic volatiles, which is a perfect fit for the environmental protection trend.
In the application of bamboo wood products, light-curing bamboo wood coatings show their strengths, mainly focusing on three key aspects: dip coating, filling and overprinting. According to the use of scenarios and quality requirements, it is subdivided into wood composite floor coatings, veneer coatings, as well as varnishes, color paints and other categories. On the coating method, roller coating dominates, supplemented by spraying, dripping and other diversified ways.
In-depth exploration of light-curing bamboo wood coating categories, each with its own unique characteristics. Let’s start with UV bamboo wood putty paint, which is like a “beautician”, specializing in rough surface wood “facelift”. Like particleboard, fiberboard, such as poor flatness of the wood, in its careful carving, small holes and tiny defects are filled one by one, the substrate surface to be sealed, the subsequent application of decorative coatings will be able to evenly adhere to create a smooth and flat appearance. This putty paint is essentially a paste, rich in ingredients, in addition to the conventional “class” of light-curing coatings – photoinitiators, oligomers, active diluents, but also incorporates a large number of inorganic fillers. Selection of fillers, but a fine job, not only to ensure that the curing rate of the impact of small, but also to have a low refractive index, easy to sand and other excellent characteristics. Talc, calcium carbonate and a host of other inorganic fillers are on the scene, each with its own capabilities. Unsaturated polyester system of UV putty paint cost-effective, affordable; acrylic system of resins and monomers is like a catalyst, greatly improving the curing speed, so that the coating appearance of thin but not lose the fullness.
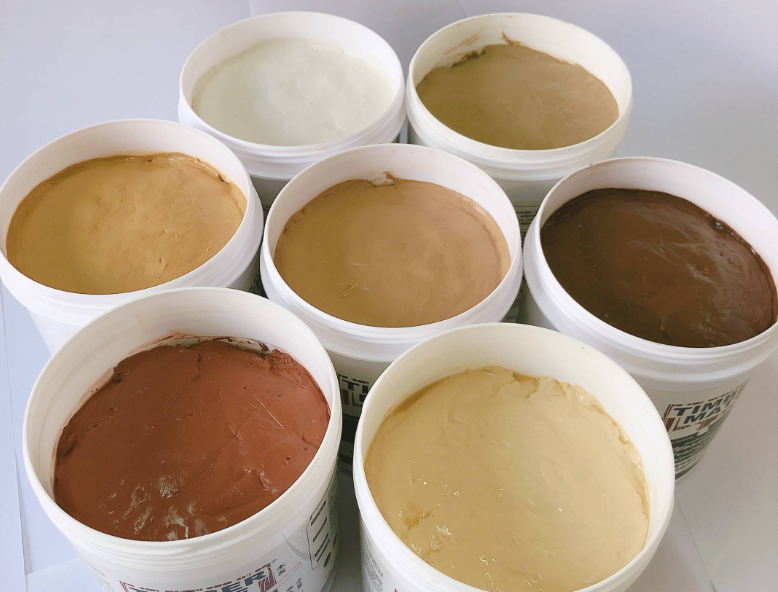
UV curing putty reference formula
UV Bamboo Primer and UV Putty have their own roles to play. While UV Putty focuses on rough woods, UV Primer focuses on relatively smooth and flat woods. It contains fewer inorganic fillers and has a lower viscosity, similar to a UV topcoat. When a layer of UV primer gently covers the surface of the wood, the low viscosity makes it like a nimble elf, quietly penetrating into the wood’s tiny pores, and with the help of film refraction, the natural beauty of the wood grain and pore structure is skillfully retained and enhanced. After UV light curing, sandpaper sanding, UV topcoat cover curing and other processes are completed in one go, ultimately presenting the perfect effect of flat, smooth and full. It is worth mentioning that the inorganic putty in the UV primer and the same kind of product in the UV putty coating, although the role is similar, but in the subtle differences, together for the coating of the solid “escort”. The sanding process is also indispensable. It is like a link that strengthens the adhesion between the coatings, so that the topcoat adheres steadily and eliminates the risk of peeling off. In addition, a small amount of zinc stearate can be used to lubricate the sanding process and prevent “white haze” during sanding. However, inorganic fillers must be used with care, as many of the metal salts of stearic acid have a weak matting effect, and fillers with a high refractive index may interfere with the curing properties, which must be taken into account.
UV curing putty reference formula
Photoinitiator ITX | 1% |
Ethyl 2-dimethylamine benzoate | 4.8% |
Bisphenol A Epoxy Acrylate | 28.22% |
TMPMA | 7.53% |
nvp | 1.88% |
Surfactant | 0.13% |
Titanium dioxide | 14.11% |
Talc | 14.11% |
Barium oxide | 28.22% |
Finally, UV Bamboo Top Coat is unique in its composition in that it eliminates inorganic fillers and is purely formulated to create a high-gloss, closed-texture finish for a wide range of applications on natural wood or wood trim. To unlock matte or frosted effects, the right amount of silica matting agent is the key “code”. Various types of acrylic paints can be precisely adapted by mixing them as needed, whether they are high-gloss or matte, colored or colorless, or different painting methods and application scenarios. It is not easy to formulate an ideal matte UV topcoat, and SiO2 with a particle size of 25 μm is often favored as a matting agent. In addition, combined processing technology opens the door to new possibilities for gloss control. Electron beam curing and UV curing work hand in hand to make the surface of the coating very fine wrinkles, matte effect appeared; different types of UV light source double curing, low-pressure UV lamp preheating, and then high-pressure mercury lamps to strengthen the same can create low gloss texture, for the light-curing coatings, the artistic expression of a thick and colorful one.
Looking ahead, as light-curing technology continues to be iteratively upgraded, light-curing coatings are expected to break through more boundaries, perhaps opening up a whole new track in cutting-edge fields such as smart materials and biomedicine. Imagine, light-curing coatings can be intelligently adjusted according to environmental changes in performance, or as a biocompatible material to help human tissue repair, these seemingly unattainable vision, perhaps in the near future will be able to become a reality, let’s wait and see the light-curing coatings a more brilliant tomorrow.
Contact Us Now!
If you need Price, please fill in your contact information in the form below, we will usually contact you within 24 hours. You could also email me info@longchangchemical.com during working hours ( 8:30 am to 6:00 pm UTC+8 Mon.~Sat. ) or use the website live chat to get prompt reply.